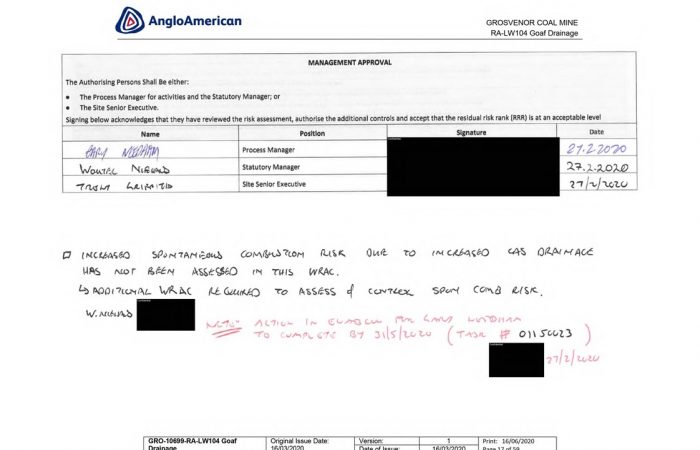
Will the Grosvenor Inquiry Recommendations actually stop another Grosvenor Style Spontaneous Combustion ignition of methane in the goaf; and/or Mineworkers being repeatedly subject to an unacceptable level of risk from explosive mixtures at the production face? History says NO
The BIGGEST Failure of the Grosvenor Inquiry was that there is little I can see which will stop another Grosvenor style incident occurring tomorrow from
a) A spontaneous combustion ignition of methane in the goaf; and/or
b) Mineworkers being repeatedly subject to an unacceptable level of risk from explosive mixtures at the production face.
https://coalminesinquiry.qld.gov.au/wp-content/uploads/2021/06/Queensland-Coal-Mining-Board-of-Inquiry-Part-II-Report.pdf
Finding 58
Coal mine workers were repeatedly subject to an unacceptable level of risk at LW 104 through mining operations being conducted in a manner that exceeded the capacity of its gas drainage, a critical control for the management of methane.
What is Recommendation 2 of getting a third party independent engineering study to decide if there has been adequate pre-drainage of methane and if there is adequate post-drainage capabilities prior to commencing each longwall panel, going to do?
Recommendation 2
Prior to the commencement of each longwall panel, coal mines arrange a review, to be validated by a third party independent engineering study:
- to ensure that adequate gas pre-drainage has been implemented, taking into account a margin for error in any predictive modelling; and
- to ensure that adequate post-drainage capabilities are in place, taking into account a margin for error in any predictive modelling.
What is this going to do?
Grosvenor was supposed to do a Risk Assessment for Spontaneous Combustion under the Coal Regulations.
The Second Workings Notice SOP states
This SOP covers the requirements of Coal Mining Safety and Health Regulation 2017 s318.
THAT NEVER HAPPENED!
Not even after the Site Senior Executive, Underground Mine Manager and Process Manager noted
Increased spontaneous combustion risk due to increased gas drainage has not been assessed in this WRAC. Additional WRAC required to assess and control spon com risk.
After all according to the Inquiry Finding 30 (q), Anglo Grosvenor Management just do not tell the Inspectors
Finding 30 q) Although there was no obligation to do so, the Inspectorate was not advised at any time that no risk assessment for spontaneous combustion associated with increased goaf drainage at LW 104 had been conducted, nor that none would be conducted until the end of May 2020, well after production commenced.
No matter what increase in residual gas emissions from LW 103
There will be increased goaf emissions until LW104 meets the install roadway of LW103 as there will be gas desorbing from 3 sides, instead of 2. Diagram below for description:
Not even the Increased likelihood of Spontaneous Combustion from oxygen ingress into the goaf when Anglo Grosvenor Management self identified that could get them to actually do the required risk assessment.
Not matter what changes they made to the post drainage system
The proposed design is modified from LW103 in three areas:
1. Significantly increased surface capacity to drain and flare goaf gas
2. Increased density of goaf drainage points (holes) along and across the longwall
1.10 Introduction
The design of LW104 goaf gas management is based on a review of LW103 gas experience, anticipated changes in the LW104 gas reservoir and aspirational peak longwall tonnage.
The proposed design is modified from LW103 in three areas:
1. Significantly increased surface capacity to drain and flare goaf gas
2. Increased density of goaf drainage points (holes) along and across the longwall
3. Floor holes to prevent shearer trips associated with the Goonyella Middle Lower seam and floor holes to address potential emissions from deeper floor reservoirs around known structures.
This SOP covers the requirements of Coal Mining Safety and Health Regulation 2017 s318.
THAT NEVER HAPPENED!
The wording for independent engineering study seems to come from the Coal Mining Act Section 172 Directive which is a Directive available only to the Chief Inspector of Coal Mines.
172 Directive to provide independent engineering study
- The chief inspector may give a directive to provide an independent engineering study about—
a) risks arising out of coal mining operations; or
b) the safety of part or all of any plant, building or structure at the mine; or
c) a serious accident or high potential incident at the mine
Certainly one improvement I suppose is that there will not be any doubt that an independent engineering report has to happen.
It was certainly beyond the Chief Inspectors of Coal Mining to issue one on their own initiative no matter how many gas exceedances occurred at Grosvenor.
The need for effective pre-drainage was identified by both Grosvenor Management and the Inspectorate during during a Structured Inspection on Ventilation Standards in February 2016.
The Mine is relatively uncomplicated at present but it is anticipated that the future will present more challenging conditions especially in regard to working temperatures and effective pre-drainage of methane from Goonyella Middle seam and surrounding strata.
It was certainly beyond the Chief Inspectors of Coal Mining in May 2018 the Mines Inspectorate noted
the mine had reported 32 HPI’s since LW 102 had commenced production in January 2018. This represented 60% of all HPI’s in Queensland associated with Methane greater than 2.5% in Longwall TG.
It was also acknowledged that continued HPl’s with Methane greater than 2.5% was not satisfactory and the mine must ensure that such HPI’s are minimised, and preferably eliminated going forward.
It was certainly beyond the Chief Inspectors of Coal Mining to issue a Directive of any description let alone a S172 independent engineering study during the months of discussion over LW 104, no matter what happened with the at least 29 methane HPI‘s on LW 103.
Even when The WRAC scope included reviewing some of the following key financial and compliance risks/issues;
The scope of the WRAC was to complete a broad brush risk assessment on the proposed Goaf Drainage for Grosvenor’s LW104. The risk assessment provided an opportunity to identify any potential issues/risks that may result from the proposed design/strategy for LW104 goaf drainage system and to develop suitable controls to minimise the potential impacts.
REFERENCE MATERIALS add any additional references as required to this generic list
• Anglo Safety Golden Rules
• DME Hazard Database
• GRO-201-PRO-Risk Management
• QLD Coal Mining Safety & Health Act 1999
• QLD Coal Mining Safety & Health Regulation 2017
• QLD Mines Guidelines
• QLD Mines Recognised Standards
• Recognised Standard 02 Control of risk management practices
In amongst the findings and recommendations are the ones actually about the explosions and what the Inquiry considered the causes.
https://coalminesinquiry.qld.gov.au/wp-content/uploads/2021/06/Queensland-Coal-Mining-Board-of-Inquiry-Part-II-Report.pdf
Finding 58
Coal mine workers were repeatedly subject to an unacceptable level of risk at LW 104 through mining operations being conducted in a manner that exceeded the capacity of its gas drainage, a critical control for the management of methane.
Finding 68
The probable cause of the first pressure wave was a methane explosion in the goaf, initiated by spontaneous combustion.
Finding 70
The cause of the second pressure wave was a methane deflagration on the longwall face.
Finding 71
The probable ignition source for the methane deflagration on the longwall face was the PUR initiated heating of coal to thermal runaway, which ignited an explosible atmosphere behind the longwall in the vicinity of shield #111, resulting in a flame propagating onto the longwall face
I personally consider “THERE IS LOW RELATIVE LIKELIHOOD OF IGNITION SOURCE BEING A PUR INDUCED HEATING/SPONTANEOUS COMBUSTION” for a number of reasons fully outlined in my Grosvenor Inquiry Public Submission directly below sets outs my reasons why.
GROSVENOR MINE INQUIRY SUBMISSION Key Issue 4 Part 2
The artificial time frames in the Terms of Reference; Grosvenor Management refusing to testify and the Inquiry not calling any of the RSHQ Inspectors who attended and Inspected the Grosvenor, only a part of the story of Grosvenor spiral to disaster unfolded.
Finding 32
Specific gas emission (SGE) at LW 104 was around 25 m3/t, and greater than anticipated.
Finding 33
In the absence of pre-drainage, or other effective strategy to divert gas from surrounding seams, management of gas emissions was wholly reliant on post-drainage and ventilation
Recommendation 2
Prior to the commencement of each longwall panel, coal mines arrange a review, to be validated by a third party independent engineering study:
- to ensure that adequate gas pre-drainage has been implemented, taking into account a margin for error in any predictive modelling; and
- to ensure that adequate post-drainage capabilities are in place, taking into account a margin for error in any predictive modelling.
During the February 2016 “Audit” of the Ventilation System the Inspectors made the following observations about Grosvenor Mine
The Mine is relatively uncomplicated at present but it is anticipated that the future will present more challenging conditions especially in regard to working temperatures and effective pre-drainage of methane from Goonyella Middle seam and surrounding strata.
https://coalminesinquiry.qld.gov.au/wp-content/uploads/2021/04/19.-LW104-Goaf-Drainage-risk-assessment.pdf
SCOPE
The scope of the WRAC was to complete a broad brush risk assessment on the proposed Goaf Drainage for Grosvenor’s LW104. The risk assessment provided an opportunity to identify any potential issues/risks that may result from the proposed design/strategy for LW104 goaf drainage system and to develop suitable controls to minimise the potential impacts.
The scope included reviewing some of the following key financial and compliance risks/issues;
• Planning and design (refer to Annex Pages 1 & 2)
• Construction & Installation of the Seamgas infrastructure
• Borehole location, design, spacing’s
• Goaf Drainage capacity (considering pipe sizing, Gas Plant at Grosvenor and forecast gas make)
• Utilisation of other indirect drainage means (existing P/GM Seam drainage including SIS or UIS)
• Water management (from pipework)
• Equipment failures/management (boreholes and surface infrastructure)
• Ongoing monitoring and management of the LW103 goaf drainage system (communications, meetings)
• Surface threats and barriers (Heritage, Cultural and physical barriers e.g. river)
• Weather and access to the system for maintenance and management
• Commissioning & Decommissioning
The risk assessment was held at “the Hub” 2nd boardroom on the 15/1/20 in accordance with;
• GRO-201-PLAN-Risk Management Plan
• GRO-200-PRO-Change Management Procedure
• QDL Mine Dept: Recognised Standard 02 Control of risk management practices
• AS/NZS ISO 31000 – Risk Management
This scope was reviewed and approved by: Garry Needham
6. REFERENCE MATERIALS add any additional references as required to this generic list
• Anglo Safety Golden Rules
• DME Hazard Database
• GRO-201-PRO-Risk Management
• QLD Coal Mining Safety & Health Act 1999
• QLD Coal Mining Safety & Health Regulation 2017
• QLD Mines Guidelines
• QLD Mines Recognised Standards
• Recognised Standard 02 Control of risk management practices
Annex 1
1.4 Pre drainage
• Pre-drainage of the GM-Seam has been conducted from a combination of both SIS (owned by Arrow) and infilling of UIS drilling where required to achieve gas content of <4m3 /t for development production and <2m3 /t for Longwall production. Gas content of the GM seam is proven to be below 2m3/t outbye of CH1600 (MG104 17c/t) an no additional gas drainage has been implemented for this region.
• Pre-drainage of the P-Seam over LW104 has been conducted from SIS Boreholes drilled from Arrow. UIS drilling of the P-Seam was attempted from MG104 22c/t that resulting in 837m of drill string being stuck in the P-Seam inbye of MG104 22c/t.
• No pre drainage of the GML seam has been conducted for LW104 and is expected to release gas readily due to the GML reservoir size combined with proximity to the working seam up to approximately CH4000-2000 (MG104 20-36c/t)
Gas content from previous cores taken from 2017 onwards indicates that the P-Seam gas content varies from 4-6m3 /t at the commencement of the longwall block. There will be increased goaf emissions until LW104 meets the install roadway of LW103 as there will be gas desorbing from 3 sides, instead of 2. Diagram below for description:
Annex 2
1.10 Introduction
The design of LW104 goaf gas management is based on a review of LW103 gas experience, anticipated changes in the LW104 gas reservoir and aspirational peak longwall tonnage.
The proposed design is modified from LW103 in three areas:
1. Significantly increased surface capacity to drain and flare goaf gas
2. Increased density of goaf drainage points (holes) along and across the longwall
3. Floor holes to prevent shearer trips associated with the Goonyella Middle Lower seam and floor holes to address potential emissions from deeper floor reservoirs around known structures.
1.13 Sudden floor emissions on the LW103 faceline
Where the GML seam is ~1m from the GM floor sudden emissions have occurred causing both shearer trips at 1.25% CH4 and shearer stoppages due to an increase in the TG CH4 to >2%.
1.14 Sudden floor emission in the goaf, LW103.
On the 11th of July a sudden floor emission occurred on LW103, the event occurred south of the interburden split that defines the emission events encountered in the development headings (Figure 13) and is consistent with gas coming from the floor in the goaf. The longwall was at ~1700m chainage, the gas was reported as coming from behind 55 chock.
In general, the height of the peak relates to the gas content (and thus gas pressure) of the source reservoir, the volume of gas released relates to the size of the source reservoir. The comparatively small amount of gas released suggests the source is the GML rather than the Harrow Creek or Dysart upper seam (Figure 14).
Similar events have occurred in LW102 and In relation to the longwall emissions, the mechanism resulting in the floor emissions is related to:
1. The longwall front abutment causing shearing in the floor seams followed by bed separation and change in pore space. This allowing desorption to occur which, where the interburden is brittle and fractures underneath the longwall face or goaf, subsequently results in sudden emission.
2. Long term pre drainage of the GM seam (by Arrow) resulting in de-stressing of the GML seam and desorption of free gas. The gas however is trapped in the GML due to the very low permeability of the interburden. This hypothesis has been proposed by G and R Williams (Wilbur Systems)2
The latter is supported by anecdotal reports from Radco drillers that surges of gas occur whilst drilling in and through the GML seam. Additionally, reports of floor blowers at the MG of LW103 at 637m chainage suggest floor emissions are not limited to regions of thin GM-GML interburden
1.18 Goaf gas management
1.18.1 Increased drainage volume
On the 2nd of January the LW was at 3509mm, active goaf drainage was 2100 L/s at 35% CH4.
Between the 2nd and 16th of August a trial was conducted to maximise goaf drainage by venting gas3
. During the trial period longwall production was not interrupted by precautionary gas trips. An increase in goaf gas flow from 7800 sL/s to 10,500 sL/s was achieved with the use of 8 extra goaf wells.
Based on the observations from the trial period, the strategy of increasing total volume drained by operating more goaf holes is valid and will be implemented in LW104. Acknowledging however, that during initial longwall goaf development limited goaf holes are available. To increase the volume that can be drained goaf holes will be:
1. TG drilled at close spacing (25m)
2. MG drilled at 150m spacing
3. Twin lateral goaf holes drilled into the P seam
1.18.2 Surface capacity
Increased surface capacity is to be installed by March 2020 to enable an additional 7500 sL/s of drainage and flaring. This is in addition to existing vacuum plant capacity of 9000 sL/s and an additional 1000 sL/s blower